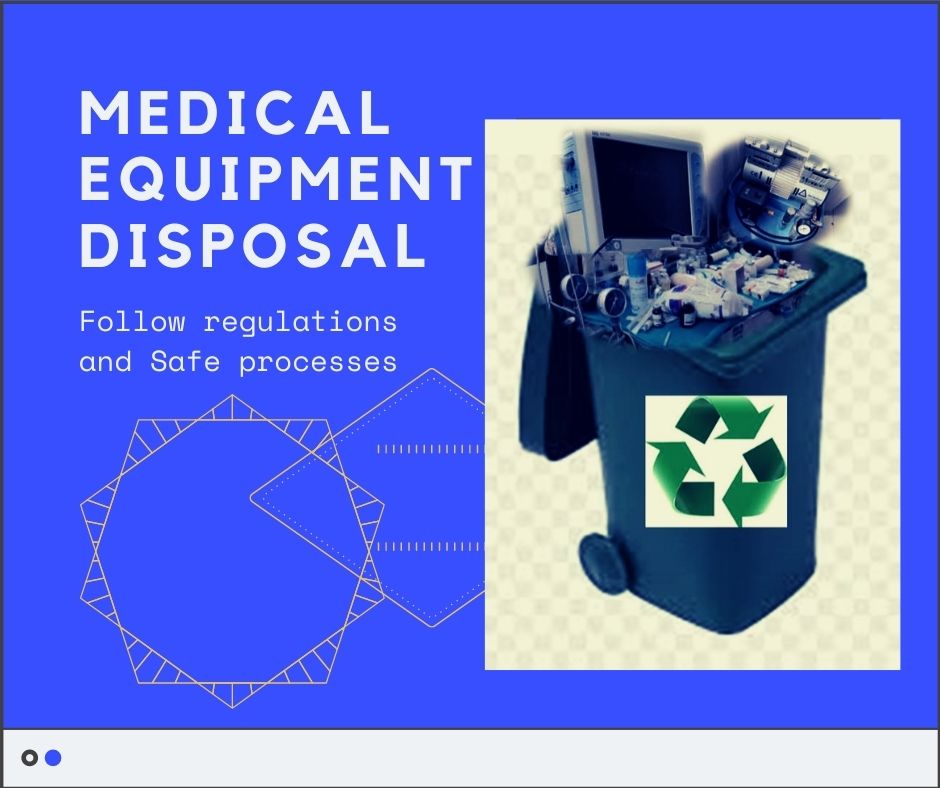
Medical equipment condemnation and disposal in a hospital can be quite a task. There is enough information available in the public domain regarding the condemnation policy & guidelines to be followed. The reasons for condemnation of medical equipment are clearly understood. As per NABH requirements there are both technical and administrative processes involved in proper disposal of condemned medical equipment. The processes are often documented well.
Still, as far as buy-back by vendors, local destruction & disposal or sale of scrap is concerned – bio-medical engineers and relevant hospital authorities are well-informed. Often there is lack of clarity when approval from appropriate authorities is required before disposal of certain medical equipment.
Here we talk about regulations that govern medical equipment disposal, appropriate authorities and approvals / NOCs / Certificate required – mainly
- Atomic Energy Regulatory Board (AERB)
- Local District Health Officer
- Certified recyclers – For Scrap Sale or disposal
Medical Equipment disposal or condemnation process
Medical Equipment disposal/ condemnation process depends largely on two considerations namely; 1) reason for condemnation and 2) whether there is alternative use for the equipment.
Reason for disposal of medical equipment
The reasons for condemnation or disposal of equipment/Instrument could be
- Cost of repairing is much higher than equipment’s worth or current value
- Technical obsolescence – Parts and service support are no longer available.
- Clinical obsolescence – The clinician user or manufacturer recommends replacement or upgrade for clinical reasons.
- Equipment that has been damaged by contamination
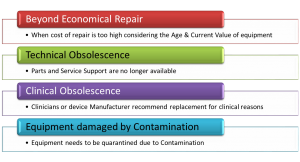
Process for Medical Equipment Disposal
First step, after deciding to condemn or dispose-off medical equipment is to remove the equipment from clinical use. If alternate use has been identified, then all service and inventory labels must be removed before transfer of asset to its new location. If any asset management system, ERP or Hospital information system is being used, data should be suitably updated.
- Alternative use of the medical equipment could be
- For Training
- For Research project etc. or
- Sale or transfer to another healthcare facility for their use.
- If the equipment cannot be used elsewhere as-is, then
- Parts can be salvaged for reuse in repair of other equipment.
- Equipment may be sent for Scrap sale.

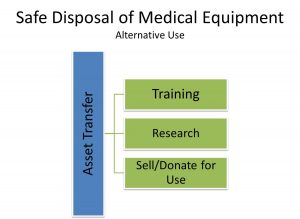
- Prior to scrapping certain safety precautions must be observed. This includes
- Removal and segregation of mercury and glass parts e.g.from BP monitors.
- Removal and segregation of lead acid, Nickel Cadmium or other alkaline batteries and electronic components (#ewaste) from patient monitors, ECG etc.
- Evacuation of Cathode ray tubes to prevent the risk of implosion from patient monitor. This is usually done by breaking-off the nipple at the back of the tube.
- Removal of in-line fuses from X-Ray or C-Arm.
- Taking-out all mains to power up the device (i.e, on hard wired devices the mains cable should be cut off)
- Disconnect all hoses able to pressurize a device (if driven by gases) such as in Boyle’s apparatus or suction pump.
- Cleaning and decontamination
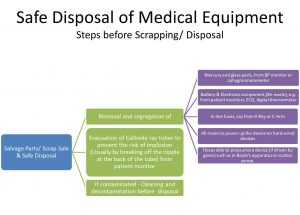
- Once the precautions have been taken equipment may be sent to scrap or incinerated where appropriate or as per the house keeping policy.
Handling Hazardous Material in Hospitals
Safety procedures must be put in place for handling Hazardous Materials. Otherwise, even during disposal of equipment staff may be accidentally contaminated or harmed. Hazardous material in a hospital could be mercury, Alcohol Based Cleaning & Disinfectant Solutions, Lubricant Sprays, Anti-Rusting Agents, Petroleum Jelly/ Grease, Adhesives like feviquik/ araldite etc.
Approval of Appropriate Authority for Medical Equipment Disposal
As mentioned before there are a few regulations that govern medical equipment disposal. Approvals / NOCs / Certificates are required before or after disposal of certain medical equipment
Appropriate Authority for Disposal of Radiology Equipment
Purchase, operation and disposal of all radiology equipment like X-Ray, C-arm, mammography, CT Scanner, Cathlab etc. are governed by AERB. Upon deciding to dispose-off radiology equipment, you need to submit “Intimation of decommissioning” for the concerned equipment through e-LORA. As per AERB Decommissioning of the X-ray equipment shall be carried out by authorized agencies with prior intimation to the Competent Authority (AERB). Authorised agencies are already registered under AERB and will follow prescribed process for safe de-activation and segregation of potentially harmful components of the X-Ray machines.
Appropriate Authority for Disposal of Ultrasound machine
Purchase, operation and disposal of all diagnostic ultrasound machines are governed by the PC-PNDT Act in India. Upon deciding to dispose-off an ultrasound machine, you must intimate the District Health Authority responsible and obtain NOC for the specific machine (serial number). District Health Authorities will trace the movement of the asset through PNDT number of the next owner of the machine, whether another user of a reseller also registered under the PC-PNDT Act, having a PNDT registration number.
Disposal of e-waste / Scrap through Certified Recyclers
One can realise some value by selling metal and other valuable components from many medical equipment as scrap. However, most of the medical equipment today are electronic equipment and have several environment un-friendly or potentially harmful or even toxic components that which if discarded carelessly can cause tremendous harm.
According to reports close to 42 million Tons of e-waste was generated in the world in 2014. Medical equipment contributes to about 8% of the annual e-waste production and it is growing. Toxins in e-waste include lead glass, batteries, as well as mercury, cadmium, chromium and ozone-depleting substances (CFCs). Electronic waste accounts for 40% of lead and 70% of heavy metals found in landfills. These pollutants are responsible for groundwater contamination, air pollution and soil acidification. Health problems associated with such toxins include impaired mental development, cancer, and damage to livers and kidneys.
Read 4R Mantra of e-waste management in medical equipment.
Before medical equipment disposal, some of the components that need special attention are:
- Batteries – Read more about disposing different types of batteries
- Cathode Ray Tubes (CRT)
- Mercury
- Glass parts
Main power supply to devices and devices with hoses capable of pressurizing devices like pumps and boyle’s machine etc. can cause accidental harm to someone if not removed and segregated before disposal. Hence they need to be handled by knowledgeable scrap dealers.
Certified e-waste recyclers follow processes to safely segregate valuable metals from PCBs, recycle batteries etc. and dispose of the other parts safely without contaminating the environment. They also provide a certificate or document for safe disposal. Hence hospital authorities responsible for condemnation of medical equipment need to work with such vendors and document the certificate for purposes such as NABH audits etc.
https://in.linkedin.com/in/shanthi-mathur-ab07838